Ball Mill For Plant Sample Grinding
2020-08-27T00:08:41+00:00
Ball Mill RETSCH powerful grinding and homogenization
RETSCH offers the largest selection of laboratory ball mills in the market! Ball mills are among the most variable and effective tools when it comes to size reduction of hard, Operation of a ball mill: Laboratory Sample Mill Sample Mill are designed for grinding particularly hard dry materials, they are similar to coffee grinders but they are more powerful and a larger and more powerful Mills Laboratory Mills2007年2月5日 Rotation of the square bottles on the roller mechanism increased the milling action by the stainless steel rods inside the bottles The rollermilling device with square A Simple RollerMill Grinding Procedure for Plant and Soil Samples
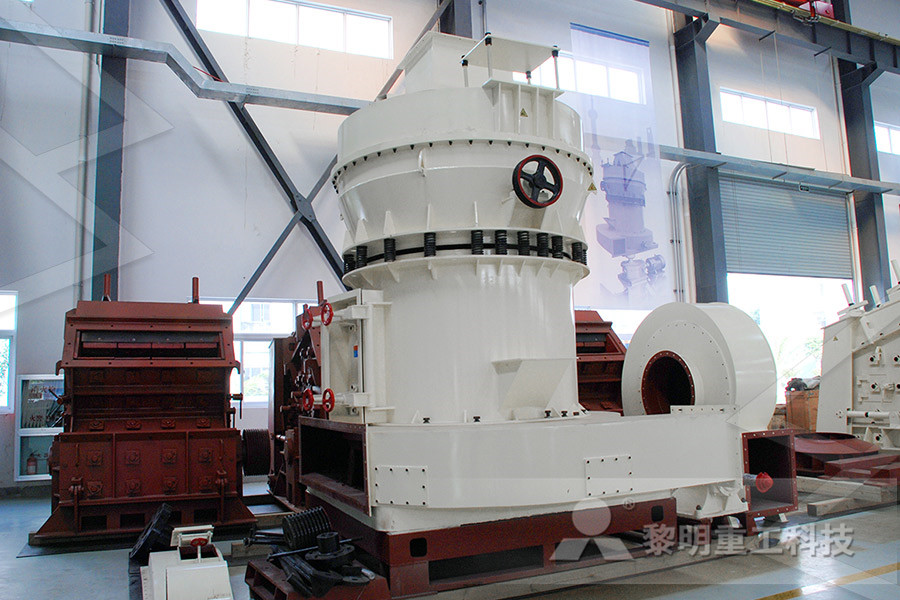
Performance optimization of an industrial ball mill for SciELO
Power consumption of the grinding mill The power consumption of the grinding mill is a critical parameter in the economics of the chromite beneficiation process The ball mill consumes about 2530% of the total energy in the beneficiation plant, and hence any improvement will improve the overall economics of the plant2021年7月12日 Over the years, alternative procedures to the Bond grindability test have been proposed aiming to avoid the need for the standard mill or to reduce and simplify the grinding procedure Some of them use the standard mill, while others are based on a nonstandard mill or computation techniques Therefore, papers targeting to propose a better A Review of Alternative Procedures to the Bond Ball Mill Standard 2020年8月19日 General Plants Sample Processing SOP h Run the mill for a few seconds to blow the last traces of the previous sample from the grinding chamber i Place a new sample bottle at the mill exit and proceed with the grinding of the next sample NB: j Ball milling is done for further fine milling samples to powder form required After thisSTANDARD OPERATING PROCEDURES

EnergyEfficient Technologies in Cement Grinding IntechOpen
2016年10月5日 The energy consumption of the total grinding plant can be reduced by 20–30 % for cement clinker and 30–40 % for other raw materials The overall grinding circuit efficiency and stability are improved The maintenance cost of the ball mill is reduced as the lifetime of grinding media and partition grates is extended 25A ball mill, a type of grinder, is a cylindrical device used in grinding (or mixing) materials like ores, chemicals, ceramic raw materials and paints Ball mills rotate around a horizontal axis, partially filled with the material to be ground plus the grinding medium Different materials are used as media, including ceramic balls, flint pebbles Ball mill Wikipedia2011年9月30日 Samples ground for 60 min by using the planetary ball mill (a and b) and 30 min by cryogenic grinding (c and d) The SEM images and perfilometric analysis showed that pellets prepared with particles obtained by both grinding procedures presented similar crater morphologies, although slight differences were found among plant speciesEvaluation of grinding methods for pellets preparation aiming

(PDF) Assessment of the Performance of Grinding Circuit for
2021年2月9日 Ball mill feed and product particle size distribution for survey 1, 2 and 3 Figure 8 to Figure 11 and Table 11 to Table 13 present the results for the size distributions and some key performance Ball Mill The proven classical option for cement grinding Whether employed as a twocompartment separator mill in an independent grinding system, or in combination with a high pressure grinding roll, the Ball Mill is a robust and reliable alternative for cement and granulated blast furnace slag grinding Used in combination with the sepol ball mill thyssenkrupp Polysius2021年3月15日 AG/SAG is more efficient than crushing and ball mill circuit for 3 of the 4 samples Abstract with quartz as the main gangue mineral Such dilution of the ore fed to the plant has demanded the inclusion of grinding stages to liberate the valuable iron oxides from the gangue, typically to sizes below about 015 mm (França et al Comparing strategies for grinding itabirite iron ores in

Kinetics of DryBatch Grinding in a LaboratoryScale Ball Mill of
2020年12月17日 The optimization of processing plants is one of the main concerns in the mining industry, since the comminution stage, a fundamental operation, accounts for up to 70% of total energy consumption The aim of this study was to determine the effects that ball size and mill speed exert on the milling kinetics over a wide range of particle sizes 2021年11月25日 In the first survey the ball mill was underperforming due to the low density in the mill, which was rectified in the second survey The ball mill was grinding to a P 80 of 50 to 70 µm, therefore the traditional Quantifying the energy efficiency of fine grinding In 1961, Fritsch GmbH registered its first patent for a laboratory planetary mill with cantilevered grinding bowls Planetary ball mills can be considered the 'workhorse' laboratory mill, ideal for rapid and lossfree grinding of laboratory samples Planetary ball mills are able to crush all manner of materials, including soft, elastic, hard Evolution of Laboratory Mills and Grinders Lab Manager
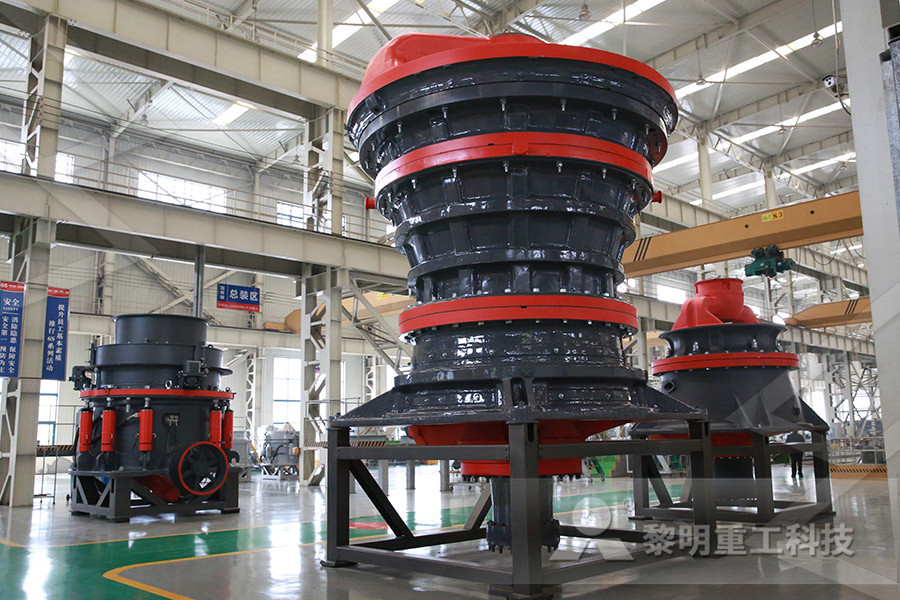
Crushers, Pulverizers, Grinders – Lavallab
Laval Lab, the onestop specialist in Milling For over 35 years Laval Lab Inc is the onestop specialist for size reduction of all types of materials We have the right crusher, pulveriser, grinder or mill for the laboratory to pilot 2007年2月5日 The rollermill provided acceptable results (soil and plant samples ranging from 16–438% C, 05–23% N, and 03777–1038 atom% 15 N (isotopic ratio analysis) had coefficients of variation ranging from 044–178, to 097–160, and 009–143, respectively) while providing an economical approach to grinding large numbers of samples to A Simple RollerMill Grinding Procedure for Plant and Soil Samples b For dry grinding, volume of the test sample is taken in such a way that the sample and the grinding media volume should always be less than 40% of total mill volume c In case of wet grinding prepare of sample of 2 kg (approx) add water to make consistency to 5560% solid by weight Here the slurry and ball will separatedAcademia BALL MILL STANDARD OPERATING PROCEDURE: SL
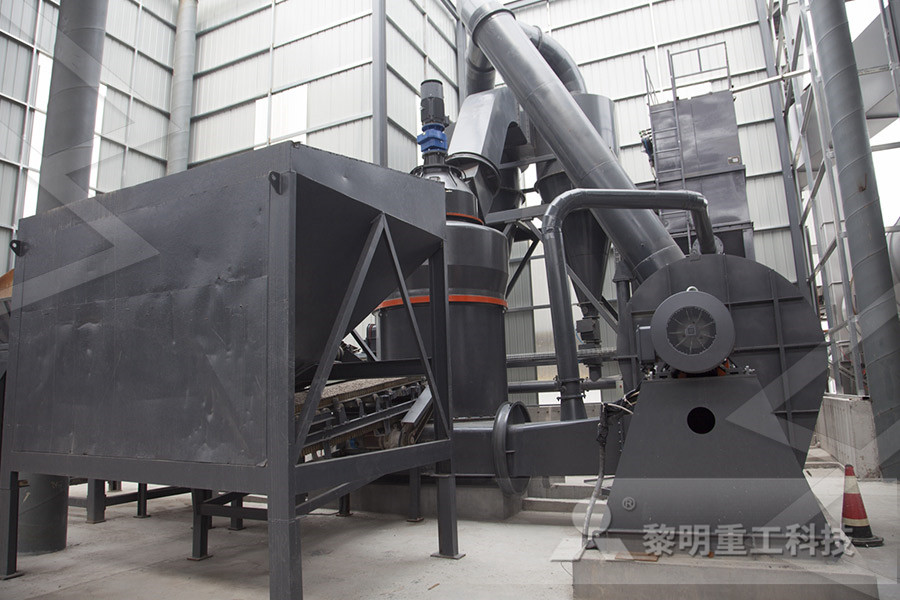
Laboratory Ball Mill for for continuous grinding operation
2023年1月30日 It could be adopted for ore grinding research and small amount of ore gringing for pilot ore dressing plant Recently an UK Graphite mining company takes an inquiry on our Laboratory Ball Mill for the above aim The structure of ball mill is mainly composed of the frame, feeding part (feeding ore bin, Swing feeder), snail feeder part, Mills and grinders are used for to break dry or wet samples into smaller particles by grinding, crushing, or cutting Blades are used in mills to cut up samples into finer particles Handheld and bench top homogenizers blend chemical or biological samples thoroughly using various methods Sonicators are homogenizers that use sound energy Grinders Homogenizers MilliporeSigmaGrinding, Mix and Cell Disruption The typical processing time of TTVB1000 is 30 seconds TTVB1000 can prepare 2 or more samples from 02ml up to 50ml It is designed as well for highsamplethroughput TTVB1000 Vibration Ball Mill is designed for processing small amount and large batch sample, for example plant, animal tissue and small Vibration Ball Mill Torontech

Ball Mill Critical Speed PDF Mill (Grinding) Cement
This paper presents a comparison of the breakage parameters with fraction of mill critical speed under the standard conditions in a small laboratory ball mill of clinker and limestone samples, which are ground at the condition 70% of critical speed of cement ball mill in Glta cement factory (lspart a/Turkey) 2 THEORY When breakage is occurring in an efficient 2023年3月9日 A ball mill is used for grinding silica sand because it is a very efficient way to reduce the particle size of the material The high energy of the balls causes the particles to break down into Why is a ball mill used for grinding silica sand?2004年12月10日 It can be summarised that for ball mills in Combigrinding plants the optimal L/D ratio is clearly below 30 For coarse feed material about 27 seems to be appropriate and about 23 for finer feed Recommendations made by Haubold (2001) who found L/D ratios in the range of 40–50 to be optimal are useful only for ball mills in Optimization of continuous ball mills used for finishgrinding of
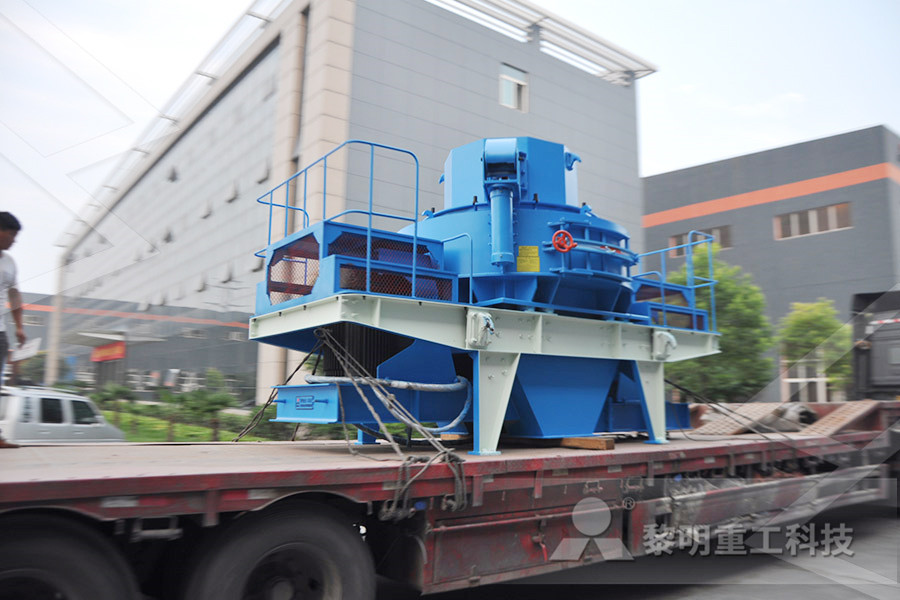
Ball Mill Ball Mills Wet Dry Grinding DOVE
DOVE small Ball Mills designed for laboratories ball milling process are supplied in 4 models, capacity range of (200g/h1000 g/h) For small to large scale operations, DOVE Ball Mills are supplied in 17 models, capacity They are conducted monthly with industrial samples to evaluate plant performance The grinding time is converted in energy by Rowland equation for small diameter mills (Rowland, 1984) Grinding conditions are summarized on Table 1 Table 1 Grinding tests conditons Test variables Conditions Average ball mill 1 Average ball mill 2 Average Comparing ball and vertical mills performance: An industrial case An iron ore concentrate sample was ground separately in a pilotscale HPGR mill in multiple passes and a dry opencircuit ball mill to increase the specific surface area of particles The effects of grinding mechanisms on generating pellet feed were assessed and pellets and DRIs were producedGrinding iron ore concentrate by using HPGR and ball mills and
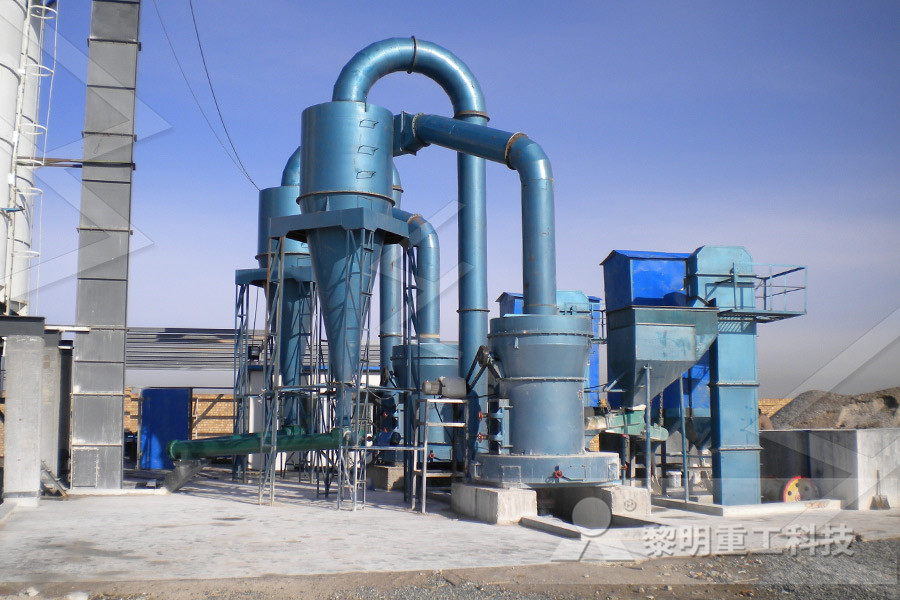
Effect of ball and feed particle size distribution on the milling
2018年6月1日 Starting with the 1700 + 850 μm size class, the measured sample together with the specified size of grinding media were then fed into the mill (Table 1) whose operating conditions are specified in Table 2 The feed material was dry batch milled for selected periods ranging from 3; 5; 15; 30–90 minThe size of the final sample depends on the ball speed, size and material The energy on impact is several times higher than conventional ball mills, giving excellent results even for short grinding times Preparing a sample for milling The grinding balls are loaded into the grinding bowl first and then the sample is added The samplePreparing a sample for milling Specac Ltdgrind plant and animal tissue for nucleic acid and protein extractions Cryoblocks can be quickly chilled in the 2600 CryoStation, and will keep samples cold during grinding to preserve RNA and proteins from heat degradation The 2650, 2660, 2662, and 2665 CryoBlocks have about the same footprintSample Grinder at Thomas Scientific
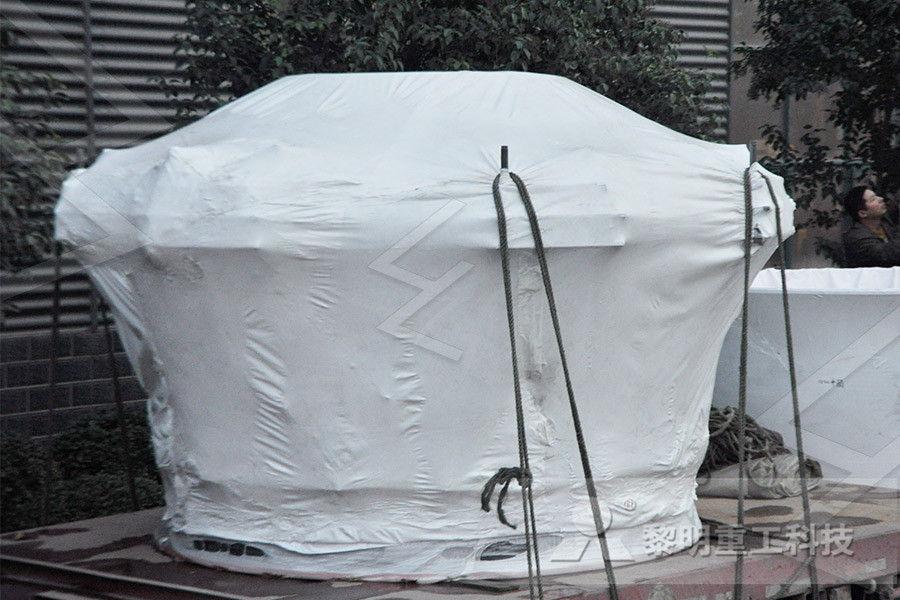
Ball milling: a green technology for the preparation and
In vibratory mills the vessel containing the sample and the grinding medium are shaken back and forth at high vibrational frequencies Important factors, in this case, are the vibrational frequency, the amplitude of vibration and the mass of the milling medium Finally, in a planetary mill the vessels are placed on a rotating2021年2月24日 There are three types of grinding media that can be used in ball mills of cement plants 1 Steel Balls Steel balls are one of the most widely used grinding media in cement ball mills, their diameters can range from 20mm to 120mm according to different grinding requirements In a cement ball mill, generally, φ50–100mm steel balls are used How to choose proper grinding media for your ball millhandled by the plant’s maintenance crew Upgrading the classifier and baghouse involves capital expenditure with a high benefit to cost ratio Optimization is especially important when multiple products are being produced Operation and Elements of a ClosedCircuit Ball Mill System Cement ball mills typically have two grinding chambersOPTIMIZATION OF CEMENT GRINDING OPERATION IN BALL MILLS

Laboratory Mills Lab Mill Used In Laboratory ANTITECK
A planetary ball mill is a necessary device for mixing, fine grinding, small sample preparation, nanomaterials dispersion, new product development, and small batch production of hightech materials The planetary ball mill for laboratory is smaller than common ball mills and mainly used in laboratories for grinding sample material down 2017年9月1日 To complement the laboratory data on shape, samples were taken from a plantscale UG2 fine grinding circuit with a ball mill and IsaMill operating in series This was to determine whether the findings relating to particle shape from the batch laboratory grinding data would be consistent with plant scale operationsFine grinding: How mill type affects particle shape characteristics 1) Scoping Study and Customized Test Planning ($9,995) In this initial scoping study, Metcom experts work with you to collect needed plant and process information, evaluate sample collection techniques and data quality, and interpret existing grinding circuit data, where possible, to form an initial opinion on the suitability of the grinding media size in Grinding Media Sizing – Metcom
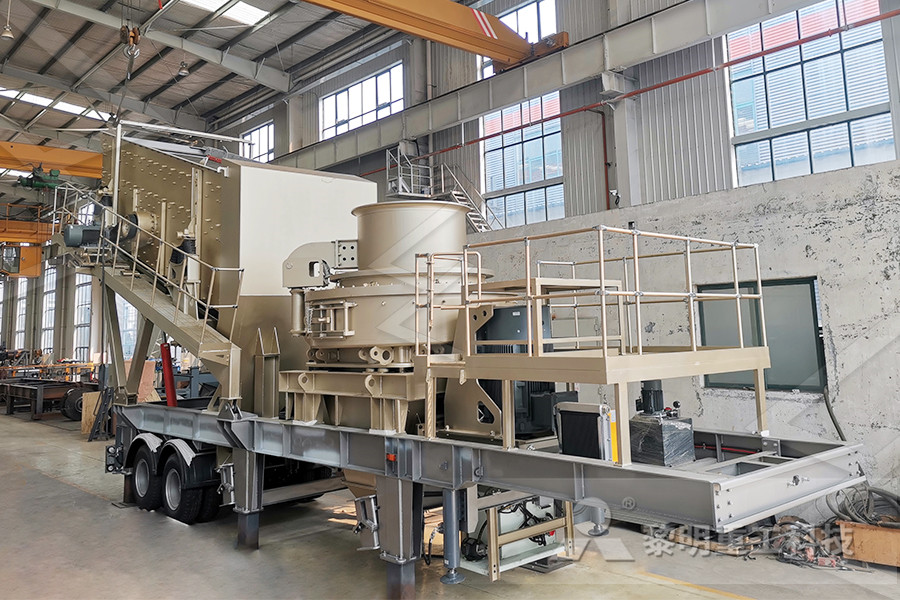
Laboratory mill, Laboratory grinding mill All industrial
PRODUCT ADVANTAGES PULVERIZATION OF LARGE SAMPLE VOLUMES The Drum Mill TM 500 is a laboratory ball mill designed to grind large sample volumes up to 35 l is the ideal Variable Speed Rotor Mill for comminution at pilot plantscale in the plastics Hammer grinding / Laboratory mill, dry sample preparation with CHpower cable, 2016年6月3日 A ball mill assisted mechanochemical extraction method was developed to extract compounds of natural product (NP) from plant using ionic liquid (IL) A small volume ball mill, also known as PastPrep (®) Homogenizer, which is often used for highspeed lysis of biological samples and for other applications, was used to dramatically increase the Ball mill assisted rapid mechanochemical extraction method for natural Mechanical Crushing and Grinding Oleg D Neikov, in Handbook of NonFerrous Metal Powders, 2009 Tumbling Ball Mills Tumbling ball mills or ball mills are most widely used in both wet and dry systems, in batch and continuous operations, and on a small and large scale Grinding elements in ball mills travel at different velocities Therefore, collision Ball Mill an overview ScienceDirect Topics

Difference Between Sag Mill Vs Ball Mill PDF Mill (Grinding
Ball Mills: Ball mill is a fine grinder A horizontal or vertical rotating cylinder which is filled partially with the balls of ceramics, small rocks and balls made from stainless steel The ball charge of a SAG mill is about 29% to 30% By friction and influence of tumbling balls inside rotating cylinderMills of varied capacity 2 kg, 5 kg 10 kg are available with recommended quantity of grinding media of assorted balls sizes Provision exists for both wet/dry grinding as a cooling jacket is provided The mill’s horizontal rotations enable the High CarbonHigh Chrome balls of different sizes bombard the sample as the mill rotatesEfficient Ball Mills for Cement Plant Quality Control insmart 2021年12月11日 The breakage and liberation of minerals are the key to fluidized mining for minerals In the ball milling process, steel balls function as not only a grinding action implementer but also energy carrier to determine the breakage behavior of ores and the production capacity of the mill When ground products present a much coarse or much The Effect of Grinding Media on Mineral Breakage Properties of

Performance optimization of an industrial ball mill for SciELO
Power consumption of the grinding mill The power consumption of the grinding mill is a critical parameter in the economics of the chromite beneficiation process The ball mill consumes about 2530% of the total energy in the beneficiation plant, and hence any improvement will improve the overall economics of the plant2021年7月12日 Over the years, alternative procedures to the Bond grindability test have been proposed aiming to avoid the need for the standard mill or to reduce and simplify the grinding procedure Some of them use the standard mill, while others are based on a nonstandard mill or computation techniques Therefore, papers targeting to propose a better A Review of Alternative Procedures to the Bond Ball Mill Standard 2020年8月19日 General Plants Sample Processing SOP h Run the mill for a few seconds to blow the last traces of the previous sample from the grinding chamber i Place a new sample bottle at the mill exit and proceed with the grinding of the next sample NB: j Ball milling is done for further fine milling samples to powder form required After thisSTANDARD OPERATING PROCEDURES

EnergyEfficient Technologies in Cement Grinding IntechOpen
2016年10月5日 The energy consumption of the total grinding plant can be reduced by 20–30 % for cement clinker and 30–40 % for other raw materials The overall grinding circuit efficiency and stability are improved The maintenance cost of the ball mill is reduced as the lifetime of grinding media and partition grates is extended 25A ball mill, a type of grinder, is a cylindrical device used in grinding (or mixing) materials like ores, chemicals, ceramic raw materials and paints Ball mills rotate around a horizontal axis, partially filled with the material to be ground plus the grinding medium Different materials are used as media, including ceramic balls, flint pebbles Ball mill Wikipedia2011年9月30日 Samples ground for 60 min by using the planetary ball mill (a and b) and 30 min by cryogenic grinding (c and d) The SEM images and perfilometric analysis showed that pellets prepared with particles obtained by both grinding procedures presented similar crater morphologies, although slight differences were found among plant speciesEvaluation of grinding methods for pellets preparation aiming

(PDF) Assessment of the Performance of Grinding Circuit for
2021年2月9日 Ball mill feed and product particle size distribution for survey 1, 2 and 3 Figure 8 to Figure 11 and Table 11 to Table 13 present the results for the size distributions and some key performance Ball Mill The proven classical option for cement grinding Whether employed as a twocompartment separator mill in an independent grinding system, or in combination with a high pressure grinding roll, the Ball Mill is a robust and reliable alternative for cement and granulated blast furnace slag grinding Used in combination with the sepol ball mill thyssenkrupp Polysius2021年3月15日 22 Benchscale tests Comminution properties for all samples were determined according to the Bond ball mill work index (BWi), Bond crushability work index (CWi), JK Drop Weight Tests (DWT) and JK Abrasion testing (NapierMunn et al 1996)The BWi was determined following the standard test, using a closing sieve of 150 µparing strategies for grinding itabirite iron ores in

Kinetics of DryBatch Grinding in a LaboratoryScale Ball Mill of
2020年12月17日 The optimization of processing plants is one of the main concerns in the mining industry, since the comminution stage, a fundamental operation, accounts for up to 70% of total energy consumption The aim of this study was to determine the effects that ball size and mill speed exert on the milling kinetics over a wide range of particle sizes